After months of careful design planning and on-site expertise, Keller has successfully completed a unique in-tunnel grouting project for one of Melbourne’s highest profile programmes – the Metro Tunnel.
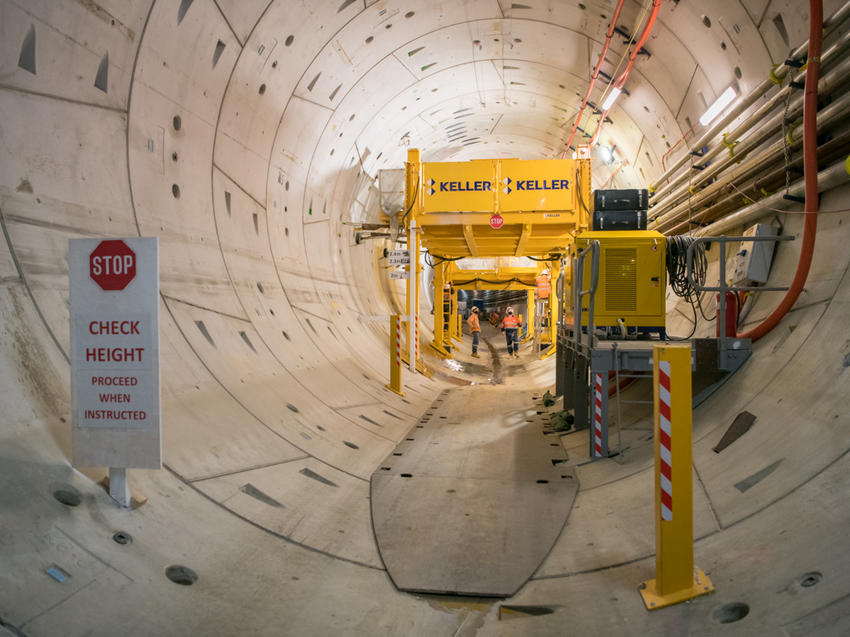
The Metro Tunnel is a multibillion-dollar infrastructure project that will untangle Melbourne’s rail network by taking some of the busiest lines underground, making it faster and easier for everyone to get around.
Over the past few years, Keller has been involved in the construction of several of the stations along the twin 9km-long tunnels, but more recently its expertise was called on for a unique and highly specialised ground improvement project.
As well as the main tunnels, a series of emergency cross-passages joining the two are also being constructed at regular intervals. But before these can be excavated, where poor ground conditions are expected, the ground requires improvement for both strength and permeability properties. It's work usually done from above ground, however, for one of the passages, that approach just wasn’t possible.
Tunnel vision
“When the contractor came to look at cross-passage 21, it was directly beneath major roads and extensive tram lines, as well as electrical services and gas mains,” explains Cliff Taylor, Keller Bid Manager and Project Manager. “To carry out these works from the surface would have been too disruptive and costly, and result in a considerable impact on the programme schedule. The only feasible option was in-tunnel grouting, but this was highly challenging, so the client turned to us.”
Over several months, Keller worked closely with contractor John Holland to develop a technical and commercially viable solution that involved drilling more than a dozen tube à manchette pipes horizontally through the wall of one tunnel and 12m to reach the other. A sodium silicate grout was then pumped through the pipes to improve the soils within and above the proposed passage, allowing the contractor to excavate without fear of collapse or water ingress.
“Crown of improvement”
“This was a very technical project with numerous challenges and risks,” says Cliff. “For example, to reach the desired treatment zone without disturbing the permanent reinforcement of the tunnels, we could only drill in specific locations on the tunnel segments. And to reach those locations in the obvert of the tunnel we required some specialised equipment.
“We designed and fabricated two jack-up working platforms specifically designed to enable a customised drill rig brought in from Italy and modified in Australia – something made more challenging due to the pandemic. Once the platform was in the tunnel, it was raised to not only allow access to the drilling locations but enable un-interrupted access for tunnel operations including full MSV access. Because of space constraints, the drill head and drill string were customised to maximise the stroke while working within extremely tight tolerances. It was then a case of drilling the tubes into the wall and injecting a sodium silicate grout that permeated the sandy clays, creating a crown of improvement.”
Drilling underground, beneath the water table, is inherently risky. But thanks to Keller’s expertise and meticulous, months-long planning, the team was able to minimise that risk. “We worked with our suppliers to customise a self-drilling TAM pipe with non-return valves and drilled through mechanical packers that cut off water in the advent of something going wrong,” he adds.
A huge team effort
After starting on site in November 2020, the team wrapped up in late March and now the cross-passage is ready to be excavated.
“This was very much a unique project with a highly customised approach,” says Cliff. “Keller has shown that we can work with a major client on a very high-profile infrastructure project to satisfy not only the technical requirements, but also the commercial ones. We’ve been able to take the client on a journey – developing a solution, overcoming many challenges and delivering on schedule, all without any safety incidents. This was a huge effort, not only from the team on the site but from all levels of our organisation.”